It may seem that a successful manufacturing company has no room for activities that don’t generate profit. However, there is one area of operation that primarily generates costs, which is why not every company chooses to maintain it. At Felgenhauer, the approach is different. This area is the Quality Department, which continues to grow and now employs 60 people.
What is Quality?
According to Plato, quality is a certain degree of excellence. While it’s hard to argue with an ancient philosopher, this interpretation leaves room for too much ambiguity.
That’s why Felgenhauer has adopted the following definition:
Quality is the ability to meet the Client’s expectations. It ensures the compliance of offered products with guidelines and applicable standards. This is achieved while prioritizing employee safety, maintaining prices acceptable to the Client, and minimizing environmental impact. Quality means the reliability and predictability of delivered products, as well as providing excellent customer service at every stage of the order process—even after its completion.
Defining the parameters of quality turns it from a mere marketing slogan into a concrete promise of the products and level of service a Client can expect.
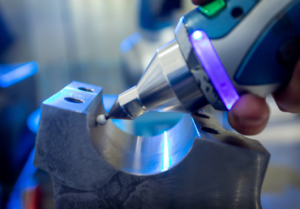

9 Benefits Delivered by the Quality Department
Let’s be honest—maintaining a Quality Department primarily generates costs. These costs include purchasing, repairing, and maintaining tools, hiring employees, and providing training. Moreover, the work of quality inspectors doesn’t directly translate into a company’s profits.
Despite this, Felgenhauer has been consistently expanding its Quality Department year after year. This is crucial from the Client’s perspective, as it provides:
- Assurance that the order meets all requirements
- Compliance with applicable standards
- Increased product durability
- Lower repair costs
- Access to comprehensive documentation
- Faster problem identification
- Customization to individual needs
- Predictability and stability
- Technical support
At Felgenhauer, the term “quality” translates into tangible benefits for the Client. So, how does the entire quality control process work?
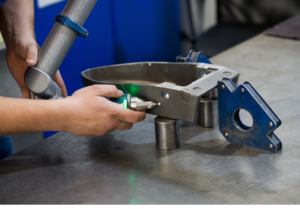
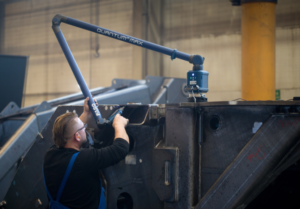
QUALITY MANAGEMENT SYSTEM
Without an appropriate system, quality is just a buzzword. It’s the implementation of regulated processes that guarantees success.
At Felgenhauer, the foundation of quality management is the ISO 9001 standard, which aims to enhance Client satisfaction by delivering products that meet requirements and regulations.
A company certified with ISO 9001 is distinguished by:
- More efficient management
- High process consistency
- Improved team communication
- Clear division of responsibilities, authority, and accountability
- Greater efficiency
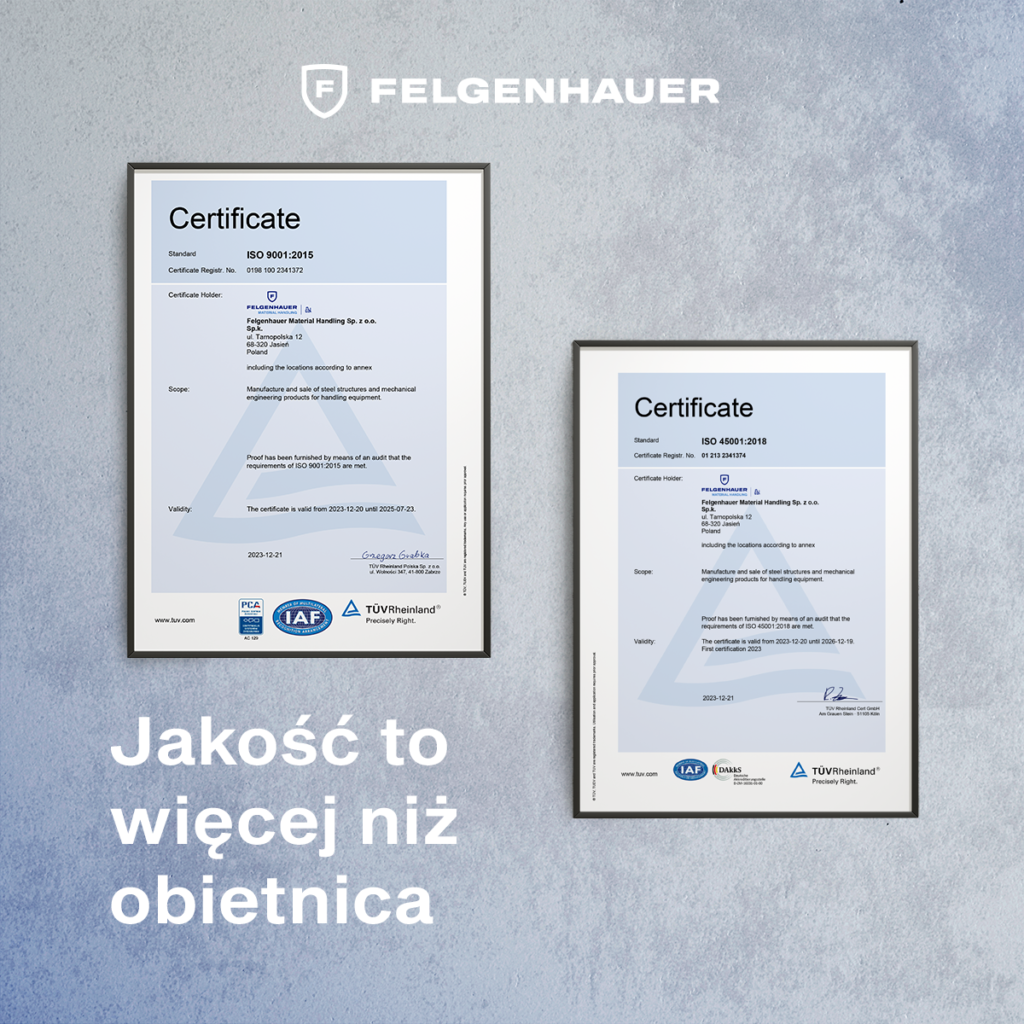
In 2023, Felgenhauer underwent an audit, earning certifications for environmental and occupational health standards:
ISO 45001 – Proof of compliance with occupational hygiene requirements, ensuring worker safety, minimizing accidents and work-related illnesses, and confirming adherence to health and safety regulations.
ISO 14001 – Evidence of commitment to environmental protection, compliance with laws, and efforts to reduce negative environmental impact.
Important:
These standards focus on even the smallest legal requirements. Compliance is the only way to earn certification, giving Clients confidence they’re partnering with a company that prioritizes all aspects of its operations.
Additionally, Felgenhauer has implemented a Japanese lean manufacturing process management system, which reduces waste and positively impacts quality. More about this system can be found [here].
HOW DOES THE QUALITY CONTROL PROCESS WORK?
Quality control begins right after materials are delivered. Certifications are verified, visual inspections are conducted, and selected batch dimensions are checked against technical drawings. In addition to general quality management systems, Felgenhauer adheres to specialized industry standards.
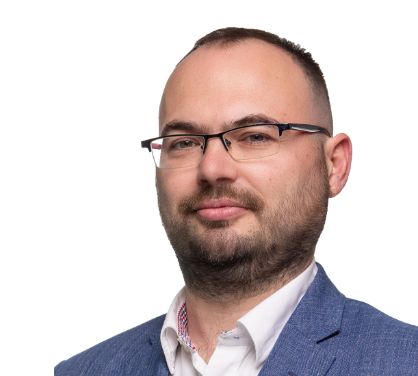
“No welded product reaches the Client without undergoing inspection. Every weld is thoroughly checked. Inspectors follow established protocols, allowing for quick product identification later,” says Jan Nowakowski, Director of Felgenhauer’s Quality Department.
When required by the project, non-destructive tests such as MP, PT, and UT (magnetic particle, penetrant, and ultrasonic testing) are conducted. For welding technology development, macro tests, hardness tests, and X-rays are also performed. Previously, these were conducted in an external lab in Zielona Góra, but Felgenhauer now has its own lab for on-site testing.
“Clients want to work with companies that have a well-developed Quality Department. In industries with significant responsibilities, it’s almost essential. That’s why they assess companies in this regard before placing orders, and Felgenhauer consistently passes these evaluations with flying colors,” adds Jan Nowakowski.
Currently, Felgenhauer employs 60 people in its Quality Department and utilizes approximately 4,000 control and measurement tools.
Important:
The company also offers the option to order a first product prototype, which undergoes the same thorough inspection process as the final product.
Traits of an Effective Quality Inspector
Those considering a career in quality control should be highly committed and well-organized. The work resembles that of a detective—once a flaw is found, the cause must also be identified.
Qualifications can be obtained through specialized external or internal training sessions. These are especially valuable, as they are conducted by individuals with extensive experience working with specific materials and processes.
Essential skills and knowledge for a quality inspector:
- Reading and interpreting technical drawings
- Data analysis
- Familiarity with applicable standards
- Proficiency in using appropriate tools
- Experience with specific processes and materials
- Patience
- Strong self-discipline
- Communication skills
- Excellent work organization
Thinking about a career as a quality inspector? Contact Felgenhauer.
Remember, knowledge and experience can be acquired. If you possess qualities suited to this role, reach out to explore development opportunities.
As you can see, the term “high product quality” encompasses much more than it seems. That’s why it’s worth understanding a company’s quality standards before starting a partnership.
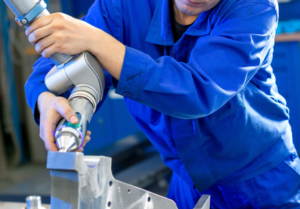
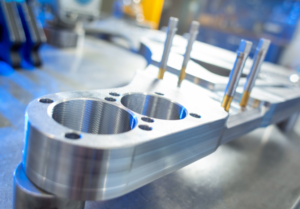