Can the tools used in production actually harm the process? Yes, if they are faulty, poorly calibrated, or improperly mapped. The solution lies in having an in-house tooling department capable of designing, manufacturing, and repairing equipment as needed. That’s exactly what Felgenhauer has implemented.
Experienced specialists, excellent workflow organization, and high-quality materials—it sounds like a recipe for success. However, without the right tools, even a small project can be challenging, let alone large-scale production. To avoid unexpected setbacks, it’s essential to address everything during the preparation phase.
We spoke with Filip Zielazny, Head of Tooling Design and Development at Felgenhauer, about how to do this effectively.
Production Tooling – Who Provides It?
Auxiliary tools are an essential part of any production process. They make work more efficient, safer, faster, and ensure the highest quality for the final product. These tools help maintain consistency by assembling and preparing the product in a predictable manner. This reduces the risk of errors and ensures the product meets design specifications.
The challenge is that every order may require completely different tooling.
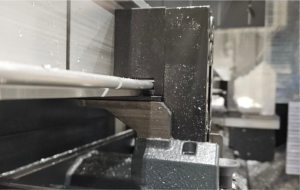
HOW CAN COMPANIES OBTAIN IT?
F.Z.: “There are three main approaches. The first is when the client provides the tools they already have. The second is sourcing them from external suppliers. Both options carry certain risks that may lead to production delays. To eliminate these risks, the third option is to commission the company handling the order to also prepare the necessary tooling.
This third approach, however, requires not just the right infrastructure but also knowledge and experience in this area. That’s why many companies still rely on ready-made solutions.”
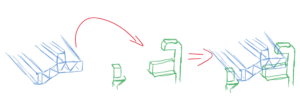
What Does the Tool Design Process Look Like?
At Felgenhauer, the tooling department is responsible for designing, manufacturing, and maintaining auxiliary tools. To date, they have completed about 500 such projects.
Most of these tools are used for:
- Tack welding
- Robotic welding
- CNC machining
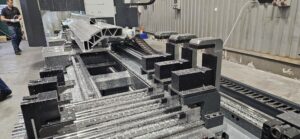
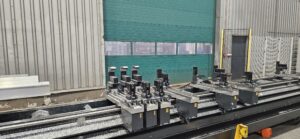
Additionally, the department produces smaller but highly valuable equipment like templates, gauges, transport trolleys, and fixtures that streamline daily operations.
F.Z.: “We either design tools based on the client’s guidelines or conduct brainstorming sessions to analyze the order and determine what will be needed. We create a list, sketch concepts, and consult with managers, welders, and CNC operators. We consider how to achieve the required production capability, estimate the cost, and calculate the lead time. Once we have all the details, we present them to the client. After their approval, we begin work.
Our advantage is that we can measure the robot or consult directly with the operator who will be using the tools at any stage. Once the tool is fabricated, it goes to the prototype department, where it is precisely measured using a coordinate measuring arm. We also check if there are any dimensional distortions caused by deformation. For example, if a part shrinks by 2 mm during welding, we can adjust the reference points in the design accordingly.
Our department is responsible for delivering a finished tool. If unique components need to be ordered, we handle it. Need painting? That’s also part of our job.”
Advantages of Having an In-House Tooling Department
The benefits of such an investment are numerous. From the client’s perspective, the key advantages include:
- Customization for every project
- High precision manufacturing
- Consultations with the production team
- Access to the machines and equipment where the tools will be used
- Direct repair and replacement of worn components
- Lower costs
- Shorter lead times
- Greater flexibility in meeting needs
- Top-notch quality
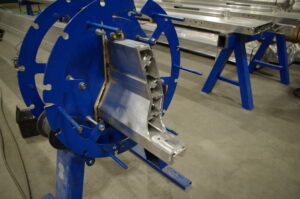
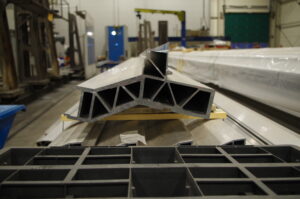
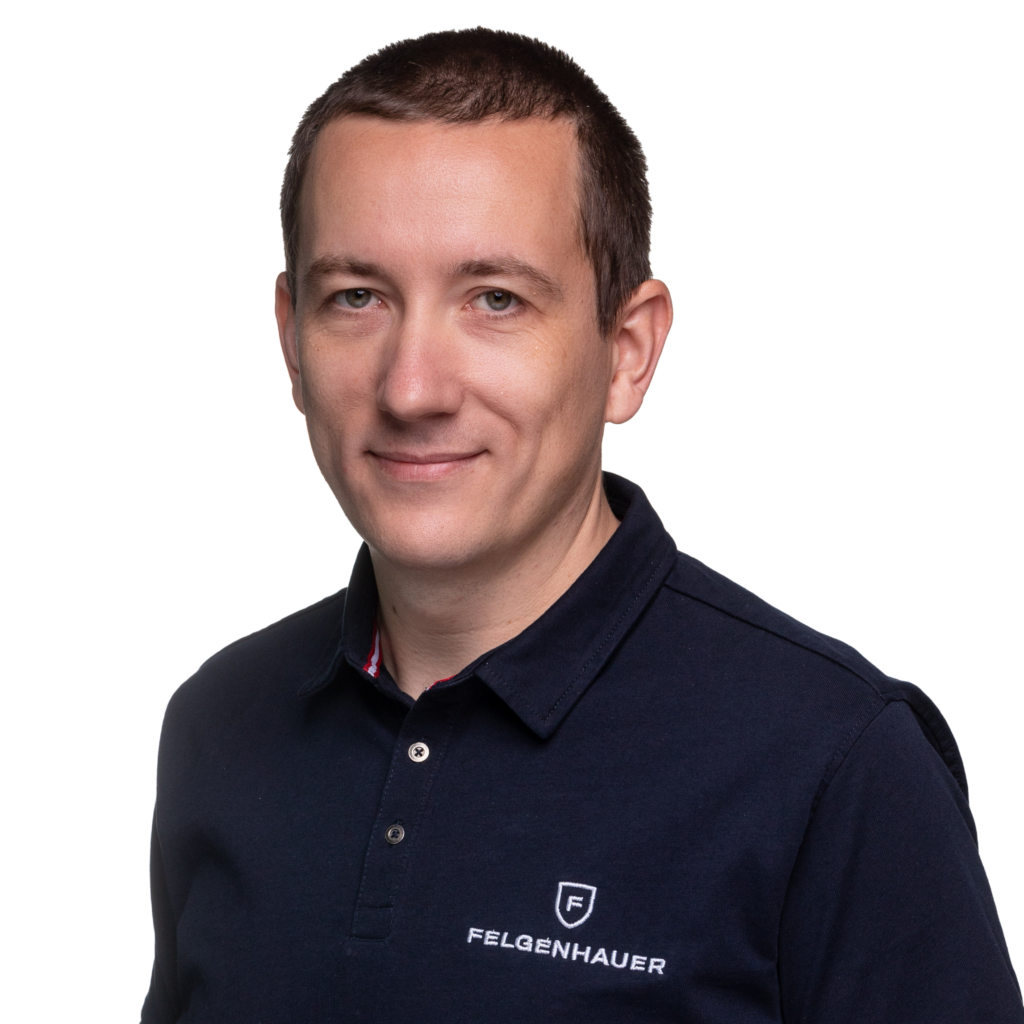
“It’s not like we make tools, send them off, and forget about them. These tools stay in our facility because they’re used in production. We build them as if they were for ourselves. We focus on quality and high interchangeability of parts because some components will inevitably wear out. Many of them can be unscrewed and replaced quickly, preventing production downtime,” explains Filip Zielazny.
AND WHEN REPAIRS ARE NEEDED…
If the client provides their own tools, any failure means sending them back for repairs. If the tools come from an external supplier, production has to wait for their service team. This downtime is wasted time. With Felgenhauer’s tooling department, this problem is eliminated, as all repairs are handled on-site.
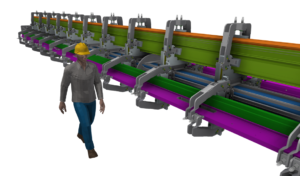
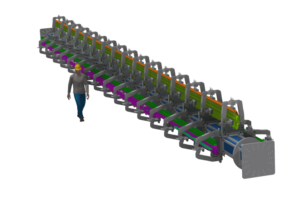
F.Z.: “Sometimes tools provided by clients are poorly measured or mapped. Once, we received a tool with a poorly designed electrical installation. On another occasion, a proposed change in the shape of a manufactured part created a risk of it hitting the floor. We can predict such issues during the design phase. What’s important is that we always ensure our tools are in proper working condition.
Clients appreciate this approach because, as they say, we are flexible, fast, and often the most cost-effective option while delivering excellent quality.”
Peter Drucker, a renowned management expert, once said, “The best way to predict the future is to create it.” He couldn’t have been more right. To ensure the success of your efforts, it’s essential to take care of every detail—even the smallest one.