Können die bei der Produktion eingesetzten Vorrichtungen dieser schaden? Ja – wenn sie defekt, ungenau vermessen oder falsch konzipiert sind. Die Lösung: Eine eigene Werkzeugbauabteilung im Produktionsunternehmen, die das Equipment entwirft, herstellt und bei Bedarf repariert. Ein solches Modell hat das Unternehmen Felgenhauer eingeführt.
Erfahrene Fachkräfte, perfekte Arbeitsorganisation, hochwertige Materialien – das klingt nach einem Rezept für Erfolg. Fehlen jedoch die richtigen Werkzeuge, wird es schwer, selbst einen kleinen Auftrag auszuführen – von Serienfertigung ganz zu schweigen. Deshalb lohnt es sich, schon in der Projektvorbereitungsphase für alles vorzusorgen.
Wie man es richtig macht, haben wir mit Filip Zielazny, dem Leiter der Abteilung für Werkzeugentwicklung und -design bei Felgenhauer, besprochen.
Produktionsvorrichtungen – Wer liefert sie?
Hilfsvorrichtungen sind ein unverzichtbarer Bestandteil jeder Produktion. Sie machen die Arbeit effizienter, sicherer, schneller und verbessern die Qualität des Endprodukts erheblich. Sie gewährleisten eine hohe Wiederholgenauigkeit, indem sie die Fertigung eines Produkts planbar und stabil machen. Dadurch wird das Fehlerrisiko minimiert, und man erhält Sicherheit, dass das Produkt den Konstruktionsvorgaben entspricht.
Das Problem: Jeder Auftrag kann völlig unterschiedliche Vorrichtungen erfordern.

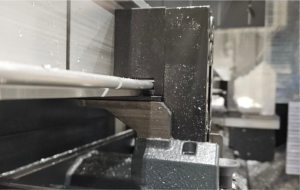
Wie können Unternehmen diese beschaffen?
F.Z. – Es gibt drei Wege. Der erste: Der Kunde stellt das Equipment selbst bereit. Der zweite: Man greift auf externe Lieferanten zurück. Beide Optionen bergen jedoch Risiken, die in späteren Produktionsphasen zu Verzögerungen führen können. Um das zu vermeiden, gibt es den dritten Weg: die Beauftragung des Unternehmens, das auch die Produktion übernimmt, mit der Anfertigung der Vorrichtungen.
Diese Variante erfordert allerdings entsprechendes Know-how und technische Infrastruktur – deshalb greifen viele Unternehmen weiterhin auf fertige Lösungen zurück.
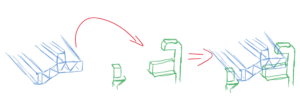
Wie läuft der Entwurfsprozess von Vorrichtungen ab?
Bei Felgenhauer ist die Werkzeugbauabteilung für den Entwurf, die Herstellung und die Instandhaltung der Hilfsvorrichtungen verantwortlich. Die Anzahl solcher Projekte liegt inzwischen bei rund 500.
Vor allem handelt es sich dabei um Vorrichtungen, die bei folgenden Prozessen eingesetzt werden:
- Heftschweißen
- Roboterschweißen
- CNC-Bearbeitung
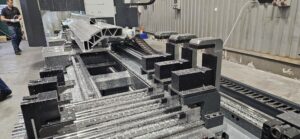
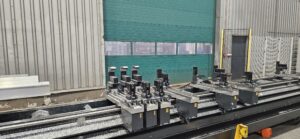
Viele davon sind kleinere Geräte (Lehren, Schablonen, Prüfvorrichtungen, Transportwagen), die jedoch im Arbeitsalltag einen großen Unterschied machen.
F.Z.– Wir entwerfen entweder nach Kundenvorgaben oder starten mit einem Brainstorming. Dabei analysieren wir den Auftrag und überlegen, was zur Umsetzung erforderlich ist. Wir erstellen eine Liste, fertigen erste Skizzen an und besprechen uns mit Managern, Schweißern, Roboter- und CNC-Operateuren. Wir prüfen, wie wir die erforderliche Produktionskapazität erreichen können, was es kostet und wie lange es dauert. Diese Informationen präsentieren wir dem Kunden. Nach Freigabe beginnen wir mit der Arbeit. Unser Vorteil: Wir können jederzeit den Roboter ausmessen oder direkt mit den Anwendern sprechen. Wenn das Werkzeug aus Metall gefertigt ist, geht es in die Abteilung für Erstmuster. Dort wird es mit einem Messarm genau geprüft. Auch mögliche Verformungen werden berücksichtigt – wenn sich ein Bauteil beim Schweißen um 2 mm verkürzt, verschieben wir die Basispunkte im Entwurf entsprechend. Wir liefern das fertige Werkzeug und kümmern uns auch um Sonderteile oder die Lackierung – das gehört bei uns dazu.
Vorteile eines eigenen Werkzeugbaus
- Individuelle Anpassung an jedes Projekt
- Höchste Präzision
- Direkte Abstimmung mit der Produktion
- Zugang zu Maschinen, auf denen die Vorrichtungen eingesetzt werden
- Schnelle Reparatur und Austausch von Verschleißteilen
- Geringere Kosten
- Kürzere Realisierungszeiten
- Hohe Flexibilität
- Höchste Qualität
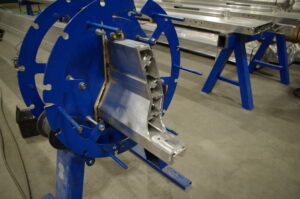
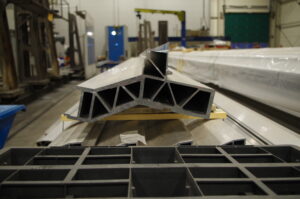
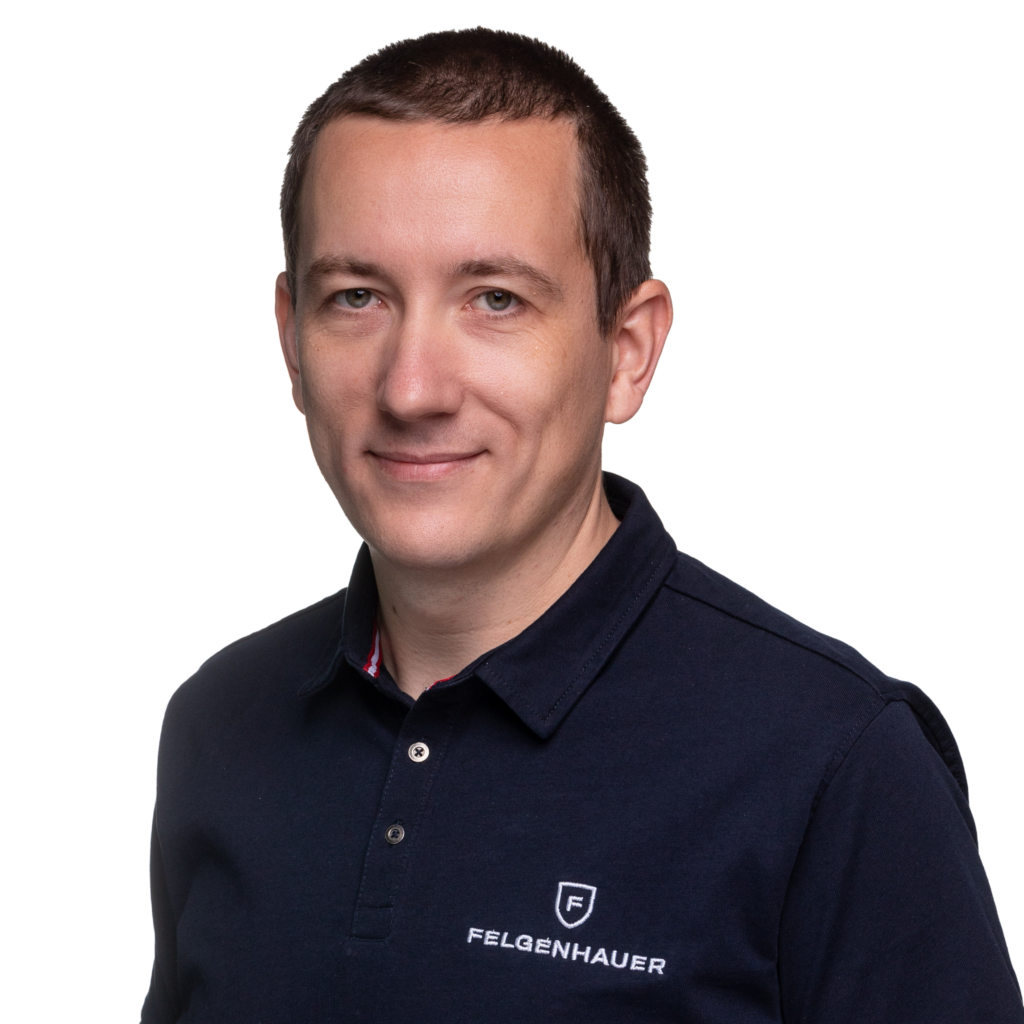
– Wir fertigen die Vorrichtungen nicht einfach, schicken sie weg und vergessen sie dann. Sie bleiben in unserer Produktion und werden dort täglich verwendet. Deshalb bauen wir sie so, als wären sie für uns selbst. Wir setzen auf Qualität und hohe Austauschbarkeit der Teile, denn Verschleiß ist normal. Viele Komponenten können einfach abgeschraubt und ersetzt werden – so vermeiden wir Produktionsstillstände. – sagt Filip Zielazny.
Und wenn eine Reparatur notwendig ist…
Wenn der Kunde eigene Vorrichtungen liefert, müssen diese im Falle einer Panne zu ihm zurück. Bei externen Lieferanten muss man auf deren Servicetechniker warten. Bis das Equipment wieder in der Produktion ist, vergeht oft viel Zeit – verlorene Zeit. Mit der Werkzeugbauabteilung von Felgenhauer entfällt dieses Problem, da Reparaturen sofort vor Ort durchgeführt werden.
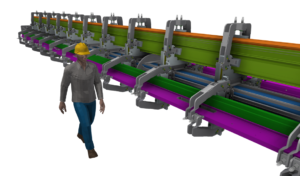
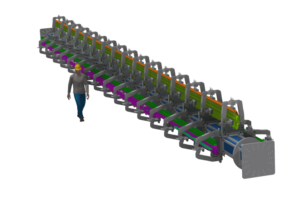
F.Z. – Es kommt vor, dass uns Werkzeuge vom Kunden übergeben werden, die nicht richtig vermessen oder geplant sind. Einmal bekamen wir ein Gerät mit fehlerhafter elektrischer Installation. Ein anderes Mal konnte durch eine Designänderung das Bauteil zu Boden fallen – dieses Risiko können wir im eigenen Entwurfsprozess rechtzeitig erkennen. Wir achten stets darauf, dass die Vorrichtungen in einwandfreiem Zustand bleiben. Unsere Kunden schätzen uns, weil wir flexibel, schnell und oft günstiger sind – und weil unsere Qualität wirklich top ist.
Peter Drucker, ein Management-Experte, sagte einst: „Die beste Methode, die Zukunft vorherzusagen, ist, sie zu gestalten.“ Und er hatte damit vollkommen recht. Wer sich seiner Ergebnisse sicher sein will, muss auf jedes Detail achten – selbst auf das kleinste.